
Case Study - The Employee Productivity equationCase Study - The Employee Productivity equation
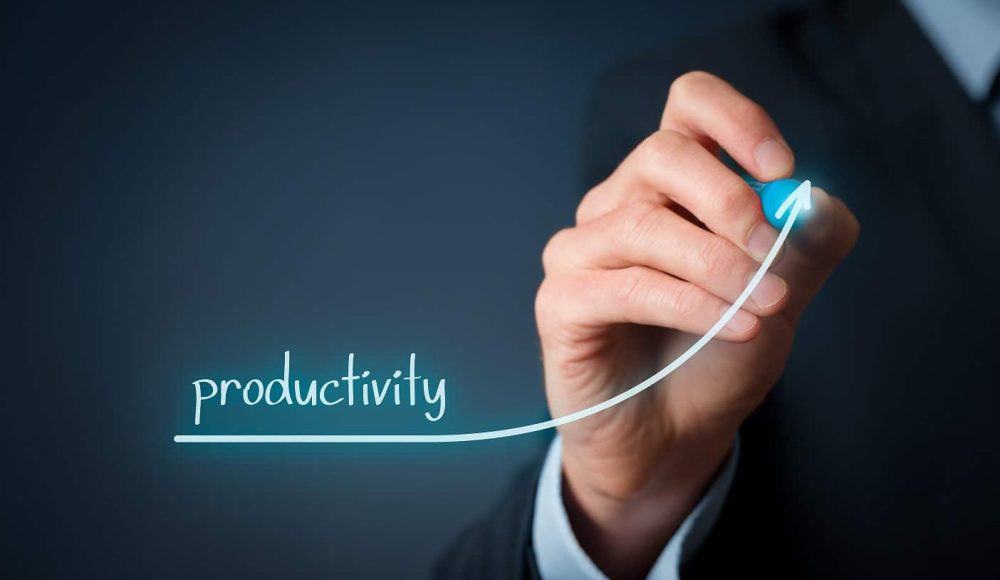
Background Background
A leading mid-sized manufacturing company, operates two plants with 350 employees. Well known for its precision products, have experienced consistent growth. However, over the past year, a noticeable decline in productivity has impacted production capacity, operational costs, customer satisfaction, and revenue.
Production Output – Declined by 15% (downwards arrow emoji ↓), Defect Rates – Increased from 3% to 6%, Overtime Costs – Up 25%( upwards arrow emoji ↑ ) , Labor costs – 10% increase (upwards arrow emoji ↑) , Absenteeism – Increased by 12% , Customer Complaints – Increased by 18% , Employee Turnover – Rose from 8% to 20.
ChallengesChallenges
SolutionsSolutions
Workforce Skill Deficiency – 37% of the workforce lacks up-to-date technical training. 42% of Employees reported misalignment between their current skills and new production technologies.

Workforce Optimization and Skills Development – Implemented a comprehensive training program to upskill 100% of employees on new machinery, automation processes, and quality control standards. Partnered with local technical institutions for specialized training in precision manufacturing.
Outcome: Increased output efficiency by 20% within six months and reduced defect rates by 50%.
Decreased Employee Engagement and Morale – Employee engagement scores fell by 25%, with workers citing about the lack of management communication, insufficient recognition, limited career growth, and dissatisfaction with working conditions as key concerns.

Employee Engagement and Retention Strategy – Introduced a structured employee recognition and reward system linked to key performance metrics such as output, quality, and safety. Implemented quarterly feedback loops, team bonding activities, employer – employee relationship enhancement and provided clear career advancement pathways to foster long-term employee retention.
Outcome: Employee engagement scores increased by 30% and reduced employee turnover to <10%.
Process Inefficiencies and Production Bottlenecks – Bottlenecks were observed in assembly and quality control processes, causing workflow disruptions. Additionally, outdated machinery in critical areas led to frequent breakdowns, further reducing output efficiency, which resulted into a 12% increase in delivery delays.

Process Automation and Equipment Modernization – Allocated capital and upgraded critical production machinery and integrated predictive maintenance systems to minimize downtime. Re-engineered assembly workflows using lean manufacturing principles to streamline operations.
Outcome: Increased production throughput by 15%, reduced downtime by 40%, and cut overtime costs by 10% within 9 months.
Health and Safety Concerns – Minor workplace incidents increased by 10%, contributing to absenteeism and fatigue. The fatigue was also linked to higher error rates,
driving up defect rates.

Health and Safety Enhancement Program – Established a proactive health and safety training module focused on fatigue management, ergonomics, and process safety. Rotated shifts to balance workload, minimize worker fatigue, and reduce incident rates.
Outcome: Reduced health-related absenteeism by 15%, contributed to smoother production operations and a 5% increase in unit output.
ImpactImpact
-
Revenue and Profitability Recovery - With improved productivity, defect rate reduction, and a more engaged workforce, the Company achieved a return of 12% annual revenue growth. Operational efficiency gained a 5% improvement in gross margins.
-
Operational Efficiency and Cost Control - Increased output efficiency by 15% within six months and scrap / rework costs reduced by 30% because of improved quality control.
-
Customer Satisfaction and Retention - Improved delivery timelines and consistent product quality increased customer retention by 10%. Customer satisfaction scores improved by 15% within two quarters.
-
Employee Engagement and Turnover - With improved morale and career growth opportunities, employee turnover declined from 20% to 8%, stabilizing workforce continuity and reduced recruitment costs by 20%.